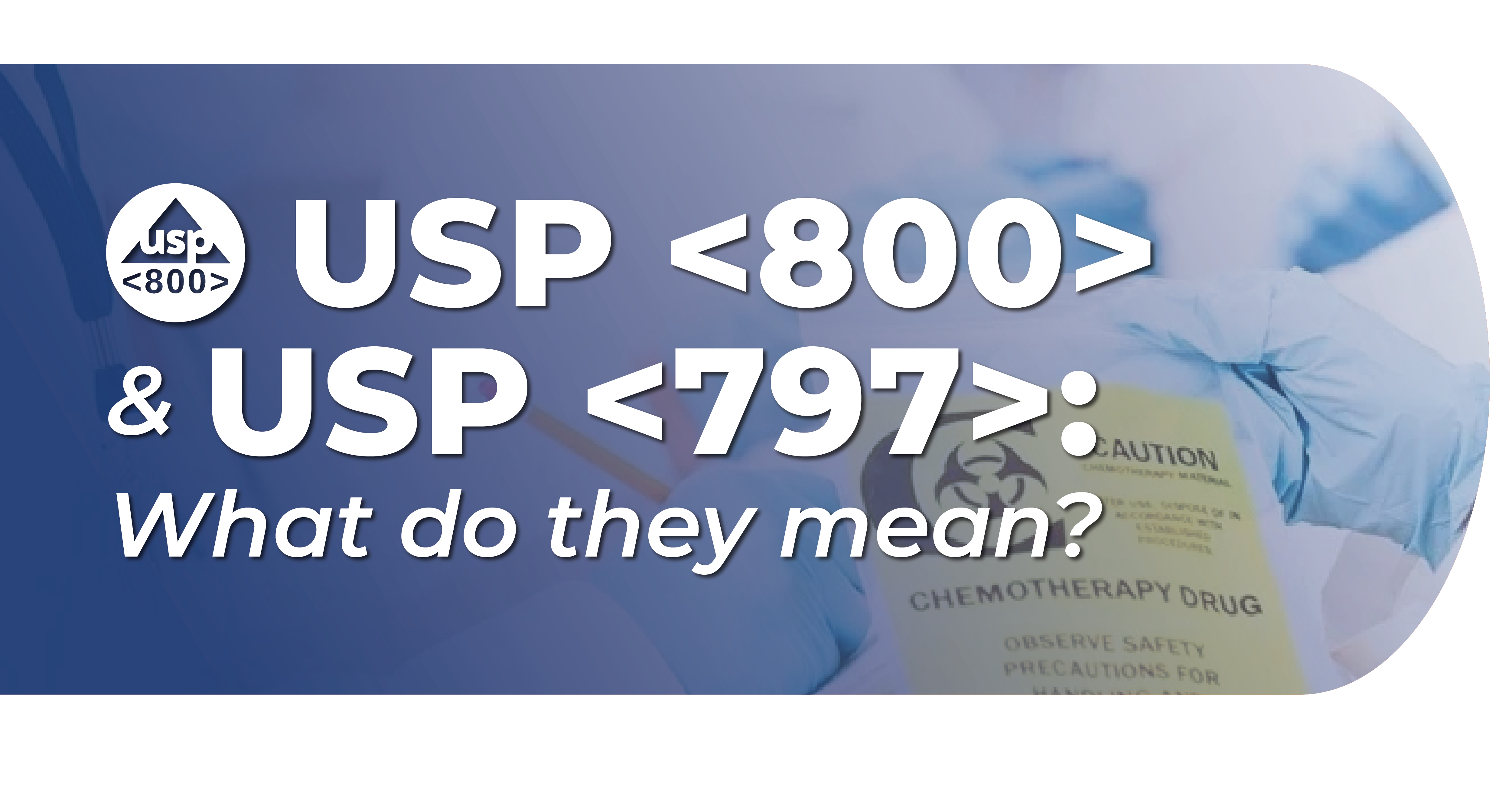
USP 800 and USP 797: What do they mean?
The United States Pharmacopeia (USP) is an organization that sets quality standards for medicines, supplements, and food ingredients in the U.S. and around the world. It ensures that products are safe, pure, and work the way they are supposed to.
These USP standards are used to determine things such as:
- Monographs: Specific rules for each drug or ingredient that tell manufacturers what it should be made of and how it should work.
- General Chapters: Broad guidelines on how to test, package, store, and compound medications, ensuring they maintain safety and quality.
- Reference Standards: Samples that show exactly how a good-quality product should look or behave, which manufacturers use to compare their products.
These standards help make sure that the medicines and supplements we buy are trustworthy and work as expected.
Compliance with USP standards is often required by regulatory authorities, including the U.S. Federal Food and Drug Administration (FDA).
Understanding USP <800>
USP <800> provides guidelines for handling hazardous drugs (HDs) in healthcare settings to protect workers, patients, and the environment, and was implemented on December 1, 2019. This standard outlines how to safely receive, store, prepare, administer, and dispose of hazardous drugs to minimize the risk of exposure in both sterile and non-sterile settings.
Hazardous drugs, as defined by the National Institute for Occupational Safety and Health, are those exhibiting one or more of the following characteristics in humans or animals:
- Carcinogenicity: Known or suspected to cause cancer.
- Teratogenicity: Known or suspected to cause congenital disabilities.
- Reproductive toxicity: Known or suspected to cause harm to reproductive organs or fertility.
- Organ toxicity: Causes toxicity to specific organs, such as the liver or kidneys, even at low doses.
- Genotoxicity: Known or suspected to cause changes in genetic material.
- New drugs that mimic existing hazardous drugs: New drugs with similar toxic properties to known hazardous drugs.
The chapter also outlines protocols, requirements, and procedures for personnel responsibilities, facility, engineering controls, and standard operating procedures.
Key Requirements:
Personal Protective Equipment (PPE): Standards for wearing PPE while handling HDs must be followed based on risk of exposure.
- Specialized gloves, gowns, head, hair, shoe, and sleeve covers.
- Eye and face protection.
- Respiratory protection when needed.
Maintain Lists of All HDs Used: Entities must maintain an updated list of all HDs used within their facilities.
- The list must be reviewed annually.
- Identify any new HDs when they enter the market.
- Complete risk assessment of HDs, including:
o Type
o Dosage form
o Exposure risk
o Packaging
o Manipulation
Identify Exposure Types: List all potential exposure based on staff activity and responsibilities, including:
- Receipt
- Dispensing
- Manipulation
- Compounding
- Administration
- Patient care activities
- Spills
- Transport
- Waste handling
Personnel Responsibilities and Training: Trained individuals must be designated to develop procedures, oversee compliance, and train all personnel handling HDs. All personnel must receive job-specific training.
Receipt of Hazardous Drugs: Healthcare entities must establish standard operating procedures for receiving HDs, including:
- HDs should be received from the supplier in impervious plastic packaging.
- Delivered to the HD storage area immediately after unpacking.
- Usage of PPE during the unpacking process.
Labeling, Packaging, Transport & Disposal: Healthcare entities must establish standard operating procedures for the labeling, packaging, transport, and disposal of HDs, as well as the use of spill kits and exposure-response training.
Deactivating, Decontaminating, Cleaning, & Disinfecting: Establish written procedures for the deactivation, decontamination, and cleaning of all areas where hazardous drugs are handled.
Administering Hazardous Drugs: Healthcare personnel must administer HDs using compliant protective medical devices and techniques while wearing the appropriate PPE.
Spill Control: Qualified personnel must contain and clean hazardous drug spills immediately while wearing appropriate PPE.
- Qualified personnel must be available at all times while HDs are being handled.
- Spill kits must be available in all areas where HDs are handled.
Medical Surveillance: Helps monitor workers for any early signs of health effects from exposure to hazardous drugs. This ongoing process includes health evaluations, follow-ups, and maintaining records per OSHA regulations.
Facilities and Engineering Controls: USP <800> requires designated areas for compounding and handling hazardous drugs, including containment primary engineering controls
(C-PEC) like biological safety cabinets, and containment secondary engineering controls
(C-SEC) such as clean rooms and buffer areas.
What is USP <797>?
Unlike USP <800>, which mainly addresses hazardous drugs in a non-sterile environment, USP <797> focuses on the standards for compounding sterile preparations. For sterile compounding of hazardous drugs, both USP <800> and USP <797> apply, meaning that sterility and safety from hazardous drug exposure must both be prioritized.
Sterile compounding involves preparing medications that must remain free from contamination, like bacteria, viruses, or any other potentially infectious microorganisms. Maintaining a sterile environment prevents contamination, which could pose harm to patients who take medications such as intravenous drugs, eye medications, or injectable treatments.
USP <797> includes guidelines for maintaining sterility, including practices related to clean rooms, equipment, and procedures to ensure that compounded sterile products are free from contamination.
Who Do They Affect?
USP <800> and <797> serve to protect the well-being of healthcare workers, patients, and the environment by aiming to ensure the safe handling of hazardous drugs and maintain quality standards and processes.
The guidelines affect personnel who handle HDs, including those in pharmacies, hospitals, clinics, physicians’ practices, and more. The guidelines also affect entities involved with storing, transporting, preparing, and administering HDs.
How Can Safetec Help You Stay Compliant?
Staying compliant with these guidelines is so important to keep people safe. Safetec can help you comply with the following products that fit the USP <800> guidelines:
- Deactivation & Decontamination: Surface Safe™ is a two-step applicator kit that cleans and deactivates chemotherapy drugs on surfaces.
- Disinfection:
- SaniZide Pro 1® is a broad spectrum, EPA Registered surface disinfectant that combines cleaning and disinfecting in one simple step with its ready-to-use, alcohol-based, hospital-grade formula.
- SaniZide Plus® Germicidal Solution is an EPA-registered disinfectant, powered by a quaternary ammonium compound, and is designed to kill microorganisms and meets OSHA Bloodborne Pathogens Standard. No diluting or mixing is required; our formula is ready to use, providing effective and safe disinfection without alcohol content.
- Hand Hygiene: p.a.w.s® Antimicrobial Hand wipes are excellent for removing germs from hands and under fingernails, formulated with 66.5% ethyl alcohol to kill 99.99% of germs.
- Spill Control:
- Safetec’s Hazardous Drugs Spill Kit is designed to mitigate risks posed to healthcare workers, patients, and the environment by swiftly addressing hazardous drug (HD) spills with its USP <800> compliant components.
- Green-Z® Solidifier is chlorine-free and safely manages hazardous spills, including chemotherapy drugs and other hazardous drugs, by absorbing and solidifying liquids, making it easier to contain spills and protect workers. We have a large variety of sizes and packaging types.
Why Safetec of America?
For over 30 years, Safetec has been a leading manufacturer of first aid, infection control, and over-the-counter products. Located in Buffalo, N.Y., all our products are manufactured and distributed by us in our state-of-the-art FDA regulated facilities.
We first entered the infection control industry with Red Z®, our flagship product, to aid in protecting against infection during the AIDS epidemic. Since then, we have expanded our manufacturing capabilities and offer five product lines of various products.