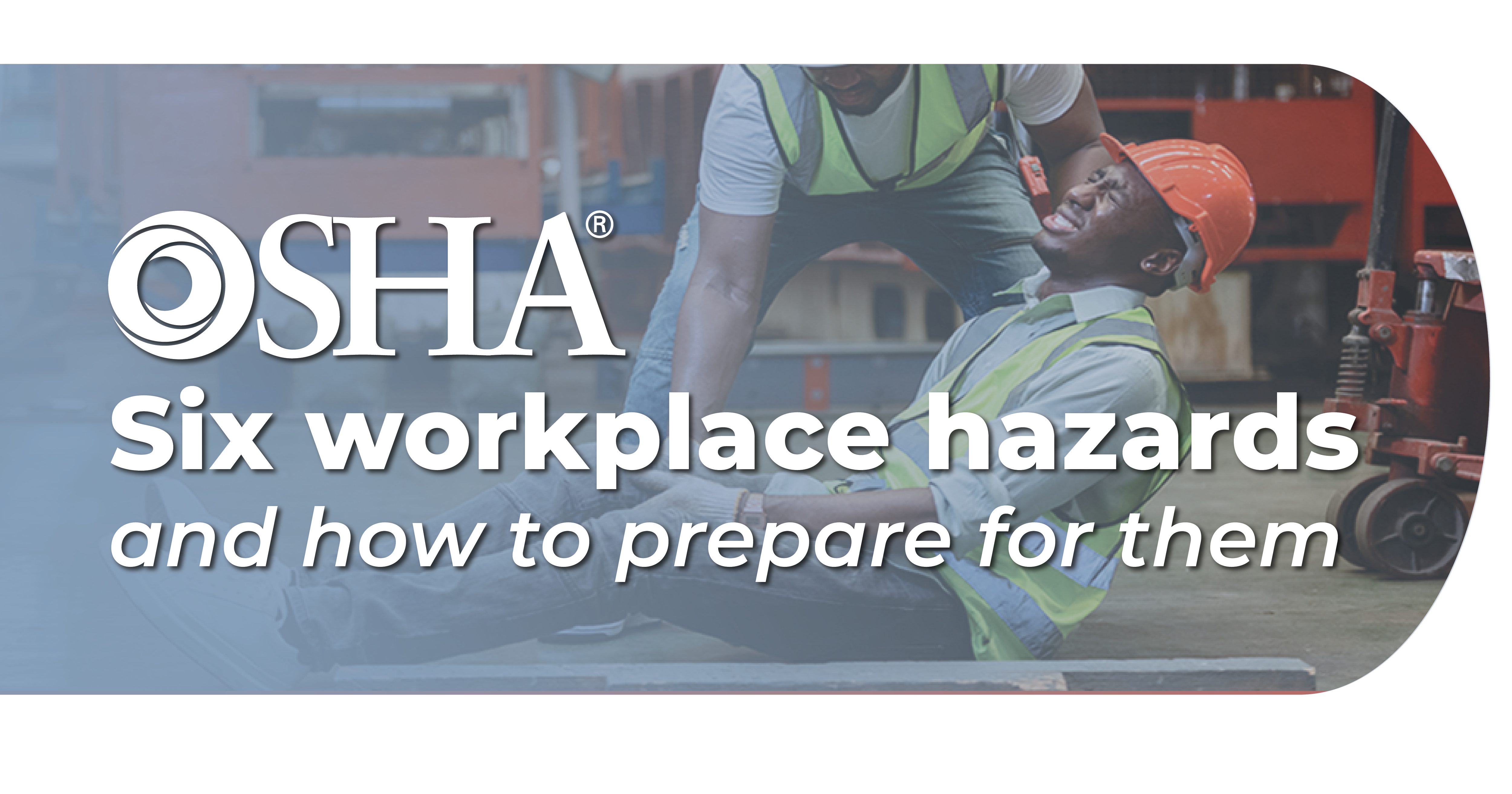
OSHA’s six workplace hazards (and how to prepare for them) 2024
If you look around your workspace or facility, you will probably notice various hazards and safety risks. Identifying all the hazards in your facility might feel overwhelming. We get it. That’s why we created a guide to help you understand the different categories of hazards, where they might be present, and how to prepare.
Biological Hazards
While we tend to associate biological hazards exclusive to specific industries, there is still a reasonable risk of exposure in almost all work environments. Biological hazards include viruses, bacteria, insects, animals, etc., that put an individual at risk of becoming ill or transmitting a disease. These health impacts can range from skin and respiratory system irritation to the transmission of infections.
To minimize biological risks, you must establish a protocol for handling biohazards and potentially infectious material. Also, make sure the required supplies, like disposable gloves, are easily accessible. Use Solidifiers to clean up blood and other bodily fluids by turning spills into a semi-solid (gel) mass, making them easy to clean up. It’s always good to have a Universal Precaution Compliance kit on hand to clean up blood and bodily fluids.
Chemical Hazards
The nature of a chemical hazard will depend on the properties of the chemicals used and kept on site. It includes both health and physical hazards, such as skin irritation, carcinogenicity, flammability, and radiation.
If your workforce uses chemicals regularly, you can keep employees safe by:
- Clearly labeling all chemicals.
- Developing a protocol for handling chemicals.
- Providing employees with the proper safety gear (respirators and gloves, for instance) to wear while in the presence of chemicals.
- Having a chemical spill kit, a hazardous drugs spill kit, and surface safe on-site to quickly and safely clean up spills that may occur.
Physical Hazards
Physical hazards are environmental factors that can harm an employee without necessarily touching them. Examples of physical hazards include:
- Electricity.
- Fire.
- Confined spaces.
- Radiation.
- Extreme temperatures.
- Consistent loudness.
- Prolonged exposure to sunlight.
Physical hazards are the hardest to detect. Reducing your employees’ risk of being exposed comes down to providing protection, such as earplugs for noisy environments or an area with shade for frequent breaks when exposed to direct sunlight.
Safety Hazards
Safety hazards are hazards that create unsafe working conditions. From falling objects to wet floors, these everyday occurrences can pose a serious risk of bodily harm. Unattended moving machinery parts pose a safety hazard as employees can sustain severe injury and fatalities. To minimize safety hazards:
- Never leave machinery unattended while in use.
- Practice safety while working from heights.
- Mandate the use of safety gear and safety apparel, like hardhats and safety glasses.
- Have your electrical wiring inspected regularly.
- Provide the proper signage (like wet floor signs) to notify employees of spills, and clean them up promptly.
Ergonomic Hazards
Ergonomic hazards are a result of physical factors that can result in musculoskeletal injuries (i.e., bones, muscles, and tendons) and are in every workplace. Such hazards include repetitive movements (such as frequent lifting), uncomfortable workstation configuration, manual handling, etc. These hazards seem small, but if not managed, have severely disabling impacts.
The best way to control ergonomic hazards is to eliminate the risk factors. You can often change the tools, equipment, or work area design to remove the hazard.
Work Organization Hazards
Work organization hazards include hazards that harm an individual’s mental health, such as harassment, workplace violence, bullying, and stress. The hazards contribute to increased absenteeism, withdrawal behavior, conflict, strain, turnover, loss of productivity, and increased risk of accidents.
Eliminating work organization hazards requires an organizational culture change.
- Make a concerted effort to address the underlying issues, and not just the symptoms.
- Commit to tackling workplace stressors.
- Foster a culture of communication between employees and their supervisors that allows open dialog about workplace stress and dissatisfaction.
- Make changes to distribute the workload better and create a calmer working environment.
Workplace safety is crucial for several reasons. A safe workplace reduces safety hazards, increases productivity, minimizes property damage, lessens a corporation’s financial losses that could result from an incident, increases employee happiness, and protects a corporation’s reputation. With all the above benefits, it’s worth taking the time to think about it.
The Safetec Solution
The world is a messy and often dangerous place. It’s essential to understand all the requirements for avoiding specific incidents and health risks to keep your employees safe, happy, and comfortable.
If you are interested in protecting your employees from the expected and the unexpected, Safetec’s in-house experts can help keep you compliant and prepared. From spill cleanup kits to solidifiers to Universal Precaution Compliance Kits, we’ve got you covered.
Shop all our OSHA compliant products here.
Updated 6/17/24